Slag inclusion
- influencing factors
- Silicon: the oxide of silicon is also the main component of slag inclusion, so the silicon content shall be reduced as much as possible.
- Sulfur: sulfide in the molten iron is one of the main reasons for slag inclusion defects in ductile iron castings. The melting point of sulfide is lower than that of molten iron. During the solidification of molten iron, sulfide will separate from molten iron, increasing the viscosity of molten iron and making it difficult for molten slag or metal oxides in molten iron to float up. Therefore, when the sulfur content in the molten iron is too high, the casting is easy to produce slag inclusion. The sulfur content of nodular cast iron should be controlled below 0.06%. When it is between 0.09% and 0.135%, the slag inclusion defects of cast iron will increase sharply.
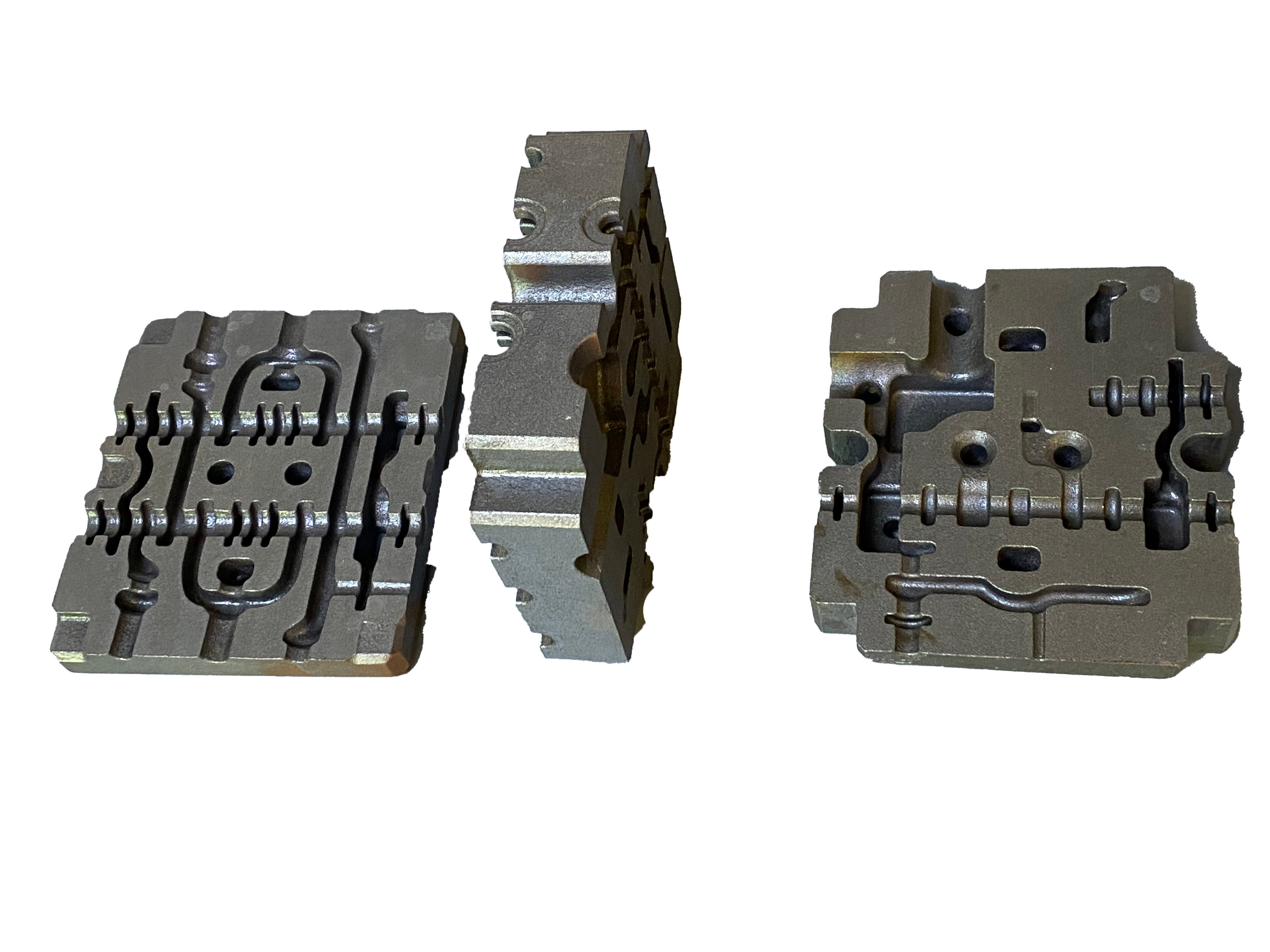
- Rare earth and magnesium: in recent years, it is considered that the slag inclusion is mainly caused by the oxidation of magnesium, rare earth, and other elements, so the residual magnesium and rare earth should not be too high.
- Pouring temperature: when the pouring temperature is too low, the metal oxides in the liquid metal are not easy to float to the surface and remain in the liquid metal due to the high viscosity of the liquid metal; When the temperature is too high, the slag on the liquid metal surface becomes too thin to be removed from the liquid surface and often flows into the mold with the liquid metal. In actual production, too low a pouring temperature is one of the main reasons for slag inclusion. In addition, the selection of pouring temperature should also consider the relationship between carbon and silicon content.
- Gating system: the gating system shall be reasonably designed with slag retaining function so that the molten metal can fill the mold smoothly, and strive to avoid splashing and turbulence.
- Molding sand: if there is excess sand or coating adhered to the surface of molding sand, they can synthesize slag with oxides in molten metal, resulting in slag inclusion; The compactness of sand mold is not uniform. The surface of the mold wall with low compactness is easy to be eroded by molten metal and forms low melting point compounds, resulting in slag inclusion in castings.
- preventive measures
- Control the composition of molten iron: try to reduce the sulfur content (<0.06%) in molten iron, and add an appropriate amount of rare earth alloy (0.1% - 0.2%) to purify molten iron, and try to reduce the silicon content and residual magnesium content.
- Smelting process: the tapping temperature of molten metal shall be increased as much as possible, and proper sedation shall be carried out to facilitate the floating and aggregation of non-metallic inclusions. Clean the slag on the surface of molten iron, and put a covering agent (perlite, plant ash, etc.) on the surface of molten iron to prevent oxidation of molten iron. Select the appropriate pouring temperature, preferably not lower than 1350 ℃.
- The pouring system shall ensure the smooth flow of molten iron, and shall be equipped with a slag collecting bag and a slag retaining device (such as a slag filter net) to avoid sand washing of the sprue.
- The compactness of the mold shall be uniform and the strong shall be sufficient; The sand in the mold shall be blown out when the box is closed.
Graphite floatation
- influencing factors
- Carbon equivalent: the carbon equivalent is too high so a large amount of graphite will be precipitated from molten iron at high temperatures. Because the density of graphite is smaller than that of molten iron, the graphite floats to the upper part of the casting driven by magnesium vapor. The higher the carbon equivalent, the more serious the graphite floatation. It should be pointed out that too high carbon equivalent is the main reason for graphite floating, but it is not the only reason. Casting size and wall thickness are also important factors affecting graphite floating.
- Silicon: under the condition of constant carbon equivalent, properly reducing the silicon content will help to reduce the tendency of graphite floating.
- Rare earth: when the content of rare earth is too small, the solubility of carbon in molten iron will be reduced, and a large amount of graphite will be precipitated from molten iron, aggravating graphite floating.
- Spheroidizing temperature and inoculation temperature: to improve the absorption rate of magnesium and rare earth elements, domestic experimental research shows that the most appropriate molten iron temperature for spheroidizing treatment is 1380 ~ 1450 ℃. In this temperature range, the absorptivity of magnesium and rare earth increases with the increase of temperature.
- Pouring temperature: generally, the higher the pouring temperature, the greater the tendency of graphite floating, because the casting is in the liquid state for a long time, which is conducive to the precipitation of graphite. A. P.druschitz and W W. Chaput found that if the solidification time is shortened, the floating tendency of graphite decreases with the increase of pouring temperature.
- Residence time: the residence time from inoculation treatment to pouring completion is too long, which provides conditions for graphite precipitation. Generally, this time should be controlled within 10min.
We are a types of cast iron skillets, cast iron dutch, john wayne cast iron wholesaler, our products satisfy our customers. And we want to be your long-term partner, any interests, welcome to contact us.